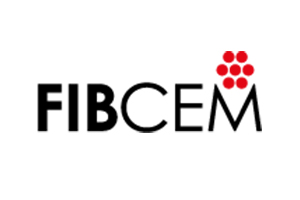
Fibre Reinforced Cement (FRC) is a durable, fire and corrosion resistant material widely used in the construction industry. Coupled with the low cost of Portland cement, these properties make it ideally suited for applications such as roofing tiles and sidings. However the production of cement is associated with a large CO2 ‘footprint’, for each tonne of cement produced nearly one tonne of CO2 is emitted. This has resulted in FRC becoming stigmatised as a ‘dirty’ material. In addition the high density of cement and hence FRC products results in high transport costs for the producers and high end user installation costs.
In order to improve the poor environmental impact of FRC and improve its specific properties, we will develop a cement based, nanotechnology enhanced material produced by a low energy consuming process. The material will consist of a cement based sandwich consisting of a foam cement core and fibre reinforced cement ‘skins’. The foam core will be produced using a nanoscale foaming agent to ensure the formation of an optimum closed cell foam structure with a micro-scale cell size with a narrow cell size distribution. Both the foam and the ‘skins’ will be reinforced with nanoclays to improve both the mechanical and transport properties of the material. The foam cement core will result in a lower density compared to existing FRC, whilst the reinforced skins will ensure the mechanical properties are improved. Added functionality in the form of decreased thermal conductivity and increased sound insulation properties will result from the foam core.
The material will be produced by a low energy multilayer extrusion process in which both the foam cement core and fibre reinforced skins are simultaneously formed such that no discontinuity is formed between them. By using a foam core and replacing part of the cement with materials such as fly ash and silica fume, the CO2 footprint of the material will be significantly reduced compared to existing FRC.
LEI activities in the Project
The Laboratory for Materials Research and Testing had leaded the development of nanoclay reinforcement in WP4 – Nanoclay Modification. Nanoclay chemistry and surface properties was investigated and the modification of these properties to enhance their compatibility and dispersion in cement based materials undertaken. The objectives of the work was the modification and surface treatment of nanoclay to optimizme cement-nanoclay particle bonding and hence the mechanical and transport properties of the FIBCEM material. Smectite type nanoclays was used and wet chemistry techniques employed to exfoliate the nanoclay material and modify the surface of the particles (intercalation) to improve compatibility with cement by ion modification and/or ion-dipole interaction.
Laboratory had worked alongside the other research partners in WP1, WP6, WP7 and WP8 investigating potential cement compositions with respect to the use of processing additives, cement replacements, polymer fibres and the effect of nanoclays and foaming agents on material properties.
Total cost: 3 780 608,60 EUR (LEI part: 167 840 EUR)
Coordinator: CEMBRIT HOLDING AS, Denmark
Participants:
- INSTITUTO TECNOLOGICO DE ARAGON, Spain
- UNIVERSITY OF BATH, United Kingdom
- LIETUVOS ENERGETIKOS INSTITUTAS, Lithuania
- DANMARKS TEKNISKE UNIVERSITET, Denmark
- ACCIONA CONSTRUCCION SA, Spain
- BRUNEL UNIVERSITY LONDON, United Kingdom
- SIKA SA, Spain
- THE UK MATERIALS TECHNOLOGY RESEARCH INSTITUTE LIMITED, United Kingdom
- LAVIOSA CHIMICA MINERARIA SPA, Italy
Project Team
Name, surname | Office | phone. | |
---|---|---|---|
LEI Representative |
|||
Jūratė Čėsnienė | |||
Project Team |
|||
Stasė-Irena Lukošiūtė | |||
Albertas Grybėnas | |||
Kristina Brinkienė | |||
Arūnas Baltušnikas | 136-LK | +37037401906 | Arunas.Baltusnikas@lei.lt |
Regina Kalpokaitė Dičkuvienė | 316-LK | +37037401984 | Regina.Kalpokaite-Dickuviene@lei.lt |
Vidas Makarevičius | 135-LK | +37037401907 | Vidas.Makarevicius@lei.lt |
Algis Makštys | 315-LK | +37037401910 | algis.1206@gmail.com |